Factory Custom Connectors
Product Overview
In today's fast-paced manufacturing industry, precision, reliability, and efficiency are paramount. One of the critical components that drive seamless operations in factories and assembly lines is the connector. These small yet powerful devices ensure secure and consistent connections between various parts of equipment, machinery, and electrical systems. In this article, we’ll explore how factory-customized connectors are transforming the manufacturing process.
Manufacturers face unique challenges in optimizing their production lines. Standard connectors may not always fit the specific needs of different machinery or processes. Custom-designed connectors are essential for achieving tailored solutions that increase productivity, enhance safety, and minimize downtime.
By working closely with connector manufacturers, factories can ensure that the products are built to withstand harsh environments, high vibrations, and extreme temperatures—conditions that are common in industrial settings. Custom connectors are engineered to integrate seamlessly into existing systems, reducing the need for frequent maintenance and repairs.
● Increased Durability: Custom connectors are designed to last longer under demanding conditions. Whether in high-speed automation, material handling systems, or heavy machinery, these connectors can handle stress without compromising performance.
● Enhanced Efficiency: With factory-specific connectors, the assembly process becomes more streamlined, with fewer issues related to incompatible parts. This leads to reduced downtime, faster setup times, and greater overall efficiency.
● Improved Safety: High-quality, factory-customized connectors ensure that electrical systems are stable and reliable, reducing the risk of malfunctions, fires, or electrical hazards that could jeopardize worker safety.
● Cost-Effectiveness: While investing in custom connectors may seem costly upfront, the long-term savings are substantial. Reduced maintenance costs, improved machine uptime, and the ability to scale up production without worrying about system failures provide excellent return on investment.
Whether you are in the automotive, electronics, or heavy machinery sector, using factory-customized connectors tailored to your production needs can significantly enhance operational performance. A connector designed for a specific application ensures smoother connections and eliminates the risk of misalignments or faulty connections, which can lead to costly delays and repairs.
Moreover, these connectors are designed to fit your unique production line requirements, allowing you to keep pace with innovation while ensuring that your systems remain reliable and optimized.
The connector is an often-overlooked yet crucial component in any factory setting. By opting for customized connectors, manufacturers can boost their efficiency, safety, and overall operational success. Collaborating with connector manufacturers to design products tailored specifically to your needs is a strategic investment that will pay off for years to come.
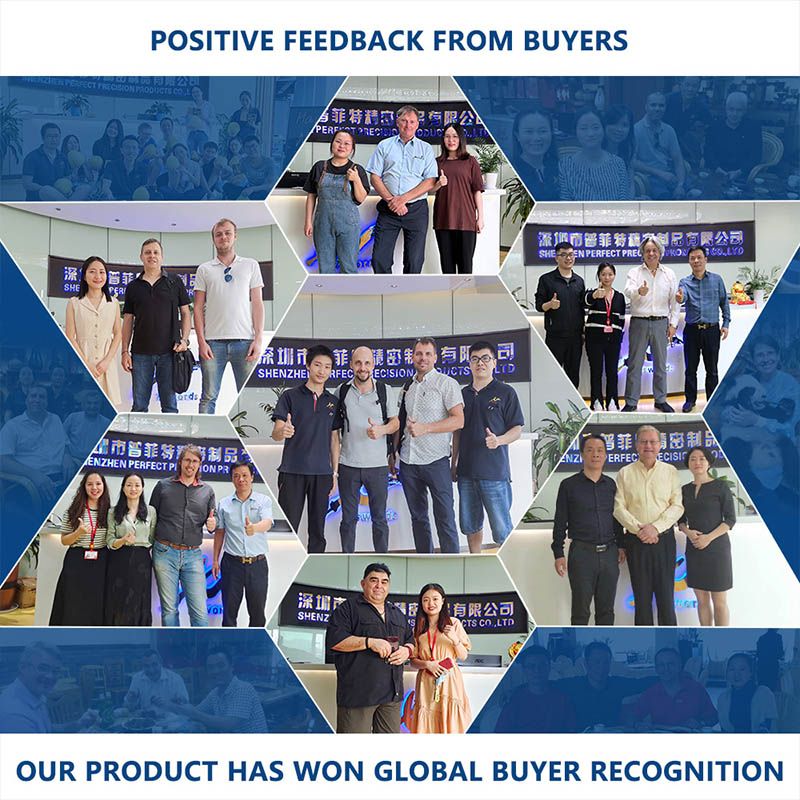
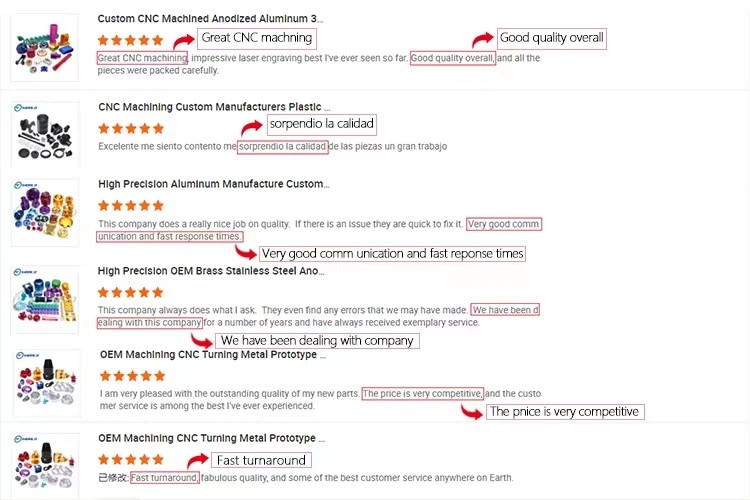
Q:What is a connector in a factory setting?
A:A connector is a component used to link two or more electrical circuits or mechanical parts together in a factory or industrial environment. It allows for seamless communication, power transfer, and data exchange between different machinery, equipment, and systems. Connectors ensure that the electrical connections remain secure and stable, reducing the risk of malfunctions or system failures.
Q:Can factory connectors be used in automation and robotics?
A:Yes, factory connectors are critical in automation and robotics systems. They ensure reliable communication between robotic arms, controllers, and other automated systems. These connectors are designed to handle high-speed data transmission, robust power requirements, and the mechanical stresses that come with automation in factories.
Q:Are custom connectors more expensive than off-the-shelf connectors?
A:While custom connectors typically involve a higher initial cost due to their tailored design, they can be more cost-effective in the long run. Custom connectors reduce the need for frequent replacements, minimize downtime, and optimize system performance, leading to fewer operational disruptions and lower maintenance costs.
Q:How do I maintain connectors in a factory setting?
A:To ensure connectors continue to perform well in a factory setting:
● Regular inspections: Check for wear, corrosion, or damage, especially in harsh environments.
● Clean connectors: Dust, dirt, and moisture can affect performance, so regularly clean connectors using appropriate methods.
● Proper installation: Ensure connectors are installed correctly, with secure connections to prevent loosening or disconnections during operation.
● Monitor environmental conditions: If your factory environment changes (e.g., humidity or temperature), ensure your connectors are capable of handling these changes.
By maintaining connectors properly, you can extend their lifespan and maintain the smooth operation of your factory’s systems.