CNC
Product Overview
In today’s competitive manufacturing landscape, precision, efficiency, and innovation are the cornerstones of success. As businesses race to meet customer demands while maintaining cost-effectiveness, Computer Numerical Control (CNC) technology has emerged as the key to unlocking next-level production capabilities. Whether you're in automotive, aerospace, consumer goods, or medical manufacturing, CNC is transforming how factories operate—boosting productivity, reducing errors, and enabling new possibilities for design and production.
CNC stands for Computer Numerical Control. It’s a process that uses computerized software to control machine tools such as lathes, mills, routers, and grinders. CNC machines are designed to follow precise instructions based on digital blueprints, producing highly accurate parts and products with minimal human intervention.
Instead of relying on manual operators, CNC machines automate the entire production process, ensuring consistency, precision, and speed. From simple designs to intricate, complex shapes, CNC is capable of handling a wide range of manufacturing tasks, making it the preferred choice for modern factories.
1. Unmatched Precision and Consistency
At the heart of CNC technology lies its precision. In traditional manufacturing methods, human operators are often the weak link in the quality chain, as errors can occur due to fatigue, distractions, or inconsistent techniques. With CNC, that variability is eliminated. CNC machines follow exact, pre-programmed instructions down to the micron level, ensuring every product that comes off the line is identical and meets strict tolerances.
This level of precision is crucial in industries such as aerospace, automotive, and medical device manufacturing, where even the smallest mistake can have serious consequences. CNC guarantees that every part, from complex engine components to intricate medical instruments, is created to the highest standards.
2. Enhanced Productivity and Efficiency
CNC machines are designed to work quickly and continuously. Unlike manual processes that rely on human operators who need breaks, CNC machines can run 24/7, producing large quantities of parts without compromising quality. Once set up, CNC machines can work autonomously, handling repetitive tasks with incredible speed and accuracy.
Additionally, CNC systems are highly automated. This reduces the need for manual intervention and streamlines the production process, which increases overall factory efficiency. CNC enables manufacturers to meet deadlines faster and ramp up production in response to changing demands.
3. Cost Savings and Waste Reduction
While the initial investment in CNC technology can be substantial, the long-term benefits are undeniable. CNC reduces labor costs by automating processes that would otherwise require manual labor. It also reduces the risk of human error, which can lead to costly reworks or scrapped materials.
Another advantage of CNC is its material efficiency. These machines cut with high precision, reducing the amount of raw material wasted during production. With fewer defects and better control over the manufacturing process, CNC technology helps businesses lower production costs and improve their bottom line.
4. Versatility and Flexibility
One of the standout features of CNC machines is their flexibility. CNC technology can work with a wide variety of materials, including metals, plastics, wood, and composites, making it suitable for virtually every industry. Whether you're producing a single prototype or running a full-scale production line, CNC machines can handle the job efficiently.
Furthermore, CNC systems can be easily reprogrammed to handle different designs. This is particularly useful for manufacturers who need to produce a diverse range of products or regularly update their designs. The ability to quickly switch between different products without changing tools or setups makes CNC ideal for industries with rapidly changing demands.
5. Automation and Reduced Labor Dependence
The shift towards automation is another driving factor behind the adoption of CNC technology in manufacturing. CNC machines can perform tasks that would otherwise require multiple operators, reducing the need for manual labor. This not only minimizes human error but also frees up valuable human resources for higher-level tasks, such as quality control and process improvement.
As factory operations become more automated, businesses can scale production more easily, adapt to market changes faster, and create higher-quality products without constantly increasing the workforce.
6. Quick Prototyping and Product Development
In industries where product development and prototyping are key to staying competitive, CNC machines are a powerful tool. CNC technology allows for rapid prototyping, meaning that manufacturers can quickly produce models of new products to test designs and functionality. This speeds up the development cycle and allows for more innovation in product offerings.
With the ability to make design changes quickly and without costly retooling, manufacturers can respond to market feedback and fine-tune their products with agility.
1.Aerospace Manufacturing
In the aerospace industry, CNC plays a crucial role in manufacturing highly precise and complex components such as turbine blades, engine parts, and structural components. With its ability to create intricate, high-tolerance parts, CNC has become indispensable for the production of reliable, durable, and efficient aircraft components.
2.Automotive Manufacturing
The automotive sector is a major beneficiary of CNC technology. CNC is used to produce parts like engine blocks, gears, chassis components, and even interiors with exceptional precision. As the demand for electric vehicles (EVs) grows, CNC’s ability to handle lightweight materials and complex shapes is helping automakers innovate and meet the needs of a rapidly changing market.
3.Medical Devices and Healthcare
CNC is transforming the healthcare industry by enabling the precise manufacturing of medical devices such as surgical instruments, implants, prosthetics, and diagnostic equipment. In a field where precision is a matter of life and death, CNC ensures that these critical products meet the strictest quality standards.
4.Consumer Electronics
Consumer electronics, such as smartphones, tablets, and wearables, require parts with tight tolerances and complex geometries. CNC machines are used extensively in the production of these devices, ensuring that components like circuit boards, connectors, and housings are manufactured to the highest standards of accuracy and durability.
5.Furniture and Woodworking
CNC is also making waves in the woodworking and furniture industries. With CNC routers and mills, manufacturers can quickly produce intricate wood designs and customized furniture pieces. The technology allows for precise cuts and high-quality finishes that would be difficult or time-consuming to achieve by hand.
As manufacturing technology evolves, so does CNC. Today’s CNC machines are increasingly integrated with smart technology, including Industry 4.0 features such as IoT connectivity, data analytics, and artificial intelligence (AI). This enables CNC systems to monitor machine health in real-time, optimize production schedules, and improve overall operational efficiency.
Furthermore, the integration of additive manufacturing (3D printing) alongside CNC is allowing manufacturers to create parts that combine both subtractive and additive processes, further pushing the boundaries of design and production.
CNC technology has proven to be the backbone of modern factory manufacturing, offering unmatched precision, flexibility, and automation. From reducing production costs to improving product quality and enabling rapid prototyping, CNC is the tool that manufacturers turn to in order to stay competitive in a fast-evolving marketplace.
As industries continue to demand higher standards of performance and quality, investing in CNC technology isn’t just an option—it’s a necessity. Whether you're looking to optimize production, improve accuracy, or stay ahead of industry trends, CNC provides the foundation for a smarter, more efficient, and more profitable manufacturing future.
Ready to take your factory operations to the next level? Embrace CNC technology and unlock the potential of precision manufacturing today.
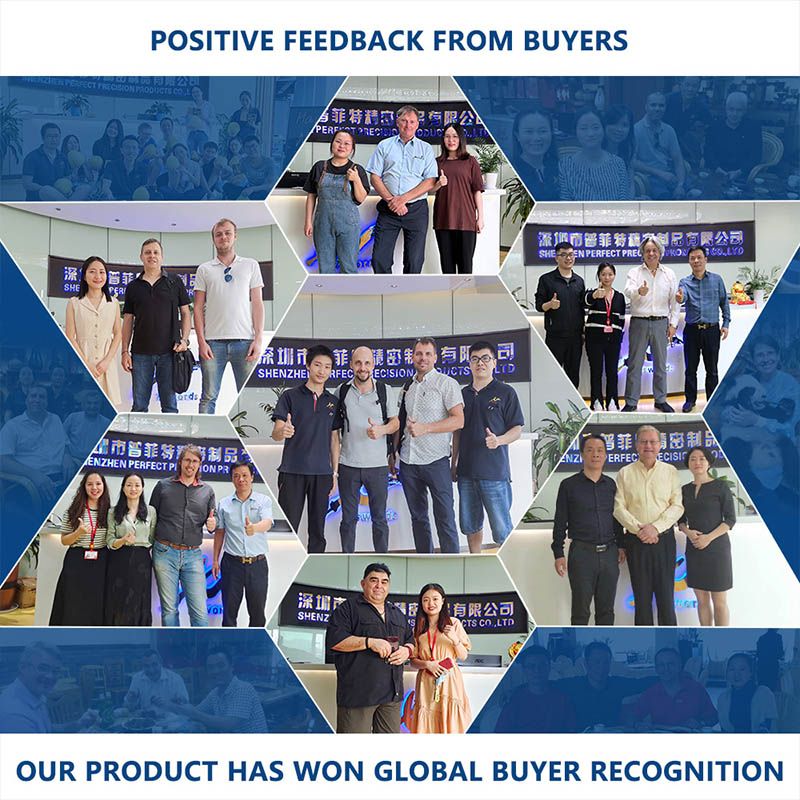
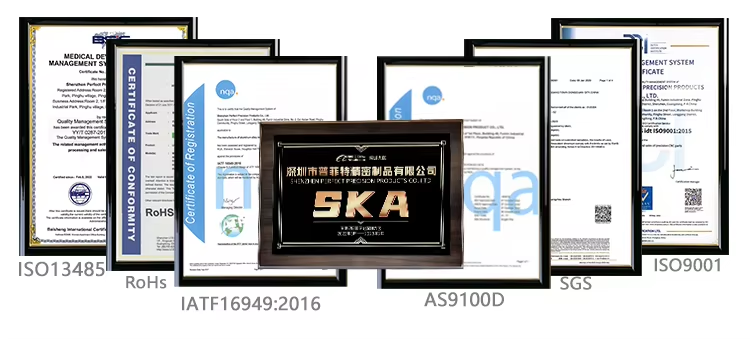
We are proud to hold several production certificates for our CNC machining services,which demonstrates our commitment to quality and customer satisfaction.
1、ISO13485:MEDICAL DEVICES QUALITYMANAGEMENT SYSTEM CERTIFICATE
2、ISO9001:QUALITY MANAGEMENT SYSTEMCERTIFICATE
3、IATF16949、AS9100、SGS、CE、CQC、RoHS
● Great CNCmachining impressive laser engraving best Ive everseensofar Good quaity overall,and allthe pieces were packed carefully.
● Excelente me slento contento me sorprendio la calidad deias plezas un gran trabajo This company does a really nice job on quality.
● If there is an issue they are quick to fix itVery good communication and fast responise times This company always does what I ask.
● They even find any errors that we may have made.
● We have been dealing with this company for a number of years and have always recelved exemplary service.
● I am very pleased with the outstanding quality or mynew parts.The pnce is very competiive and the custo mer service is among the best Ive ever experienced.
● Fast tumaround rabulous quality,and some of the best customer service anywhere on Earth.
Q:What is the difference between CNC and manual machining?
A:CNC machining is automated and controlled by a computer, while manual machining requires human skill and physical control of tools. CNC offers higher precision, speed, and repeatability compared to manual machining.
Q:Can CNC machines be used for prototyping?
A:Yes! CNC machines are excellent for prototyping because they can quickly turn CAD designs into physical models, allowing for rapid iteration and testing of new ideas.
Q:Is CNC technology suitable for small businesses or home workshops?
A:Yes, CNC technology is accessible to small businesses and even home workshops. Many companies offer compact and affordable CNC machines that can be used for small-scale production, prototyping, and custom designs.